Ideal Practices for Effective Tank Welding Inspection Processes
Wiki Article
The Necessary Function of Tank Welding Inspection in Ensuring Structural Honesty and Security Compliance in Industrial Applications
In the world of industrial applications, tank welding examination becomes an essential aspect in safeguarding architectural stability and ensuring conformity with security policies. Using a combination of strategies such as visual assessments and progressed screening methods, these assessments serve to identify and minimize prospective flaws prior to they escalate right into substantial risks. The implications of these techniques extend past mere governing adherence; they fundamentally influence operational effectiveness and property durability. The intricacies bordering the evaluation procedure prompt a closer assessment of its methodologies and results, disclosing layers of importance that benefit more expedition.Significance of Storage Tank Welding Assessment
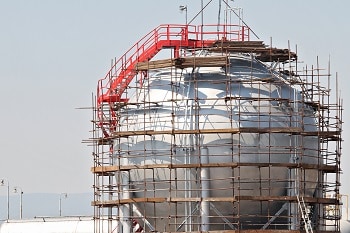
Guaranteeing compliance with sector criteria and laws is an additional considerable aspect of container welding examination. Governing bodies mandate stringent guidelines for the building and maintenance of storage space tanks, and comprehensive inspections aid organizations stick to these needs. Non-compliance can cause serious penalties, including penalties and closures, even more emphasizing the demand for extensive inspection procedures.
In addition, tank welding assessment plays an essential function in keeping operational effectiveness. In recap, the significance of storage tank welding examination lies in its capability to protect public health and wellness, shield the setting, and ensure compliance with regulative structures.
Trick Examination Techniques
Effective container welding examination counts on a range of crucial strategies that make certain thorough assessment of weld high quality and structural integrity. Among the most prevalent techniques are visual evaluation, ultrasonic testing, radiographic testing, and magnetic particle testing - Tank Welding Inspection. Each method provides one-of-a-kind benefits in analyzing various elements of the weld
Visual evaluation offers as the very first line of defense, permitting examiners to determine surface defects, abnormalities, or incongruities in the weld grain. Ultrasonic screening utilizes high-frequency acoustic waves to detect inner imperfections, such as fractures or spaces, providing a comprehensive analysis of weld integrity. This approach is especially reliable in identifying problems that may not be noticeable on the surface area.
Radiographic testing makes use of X-rays or gamma rays to produce photos of the welds, exposing internal stoppages and supplying a permanent document for future recommendation. This technique is very efficient for critical applications where the threat of failing should be decreased.
Finally, magnetic fragment testing is used to identify surface area and near-surface problems in ferromagnetic products. By applying electromagnetic fields and fine iron fragments, examiners can determine gaps that might jeopardize the architectural stability of the container. Together, these strategies form a durable structure for making sure high-quality welds in commercial applications.
Conformity With Safety Requirements
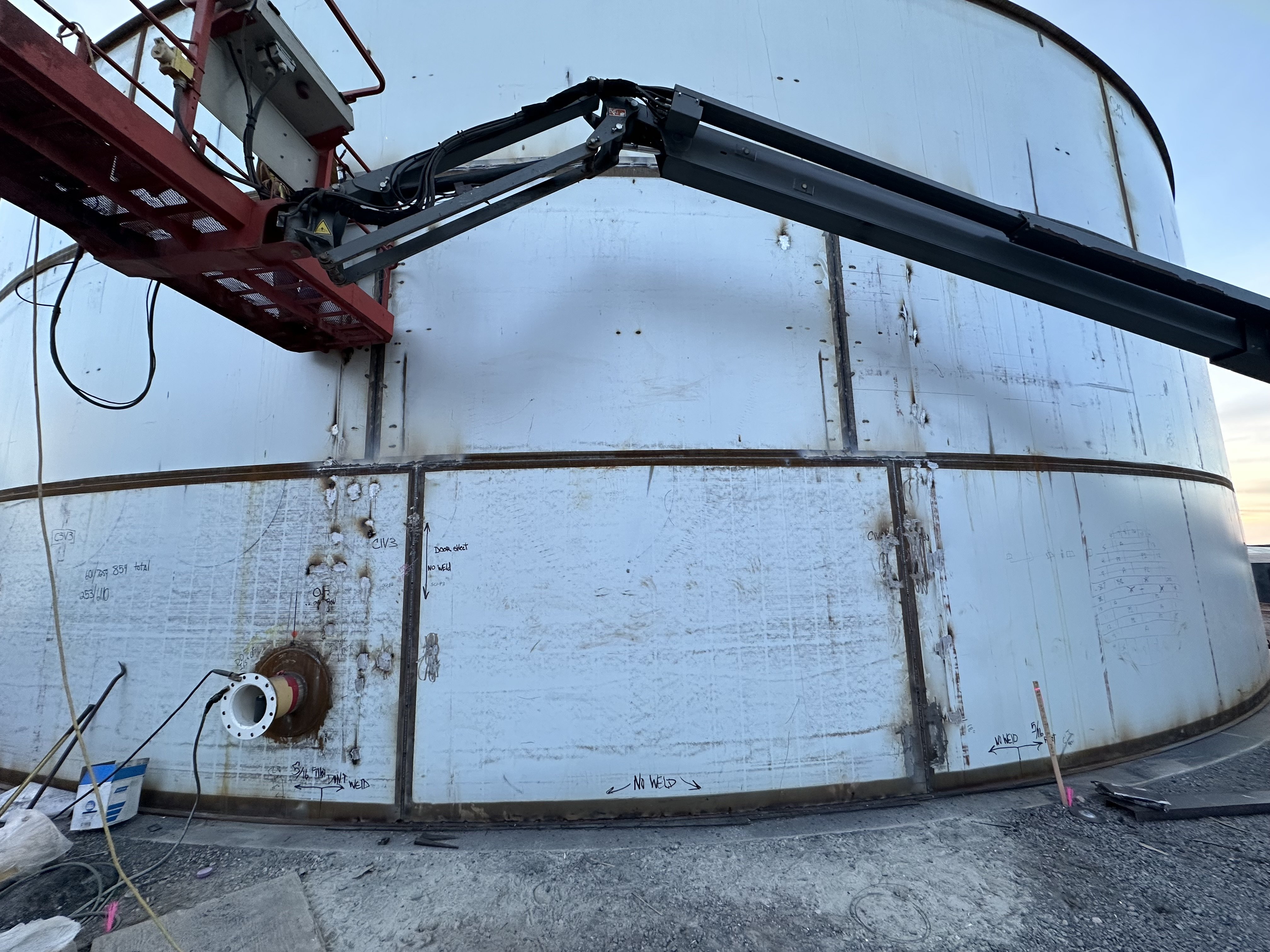
Routine assessments play an essential function in making sure compliance by determining prospective failures or inconsistencies from suggested criteria. Assessors are trained to assess weld quality, verify product requirements, and examine the total architectural honesty of containers. Their experience is essential in making sure that welding processes meet the required safety and security standards.
Furthermore, conformity with safety and security criteria not just secures workers but additionally safeguards the setting from possible hazards such as leakages or disastrous failings. Organizations that focus on security compliance are much better placed to mitigate threats, boost functional effectiveness, and foster a culture of safety and security within their labor force. In recap, maintaining rigorous conformity with safety and security requirements is vital for the successful operation of container welding tasks in commercial settings.
Advantages of Routine Evaluations
Regular examinations are indispensable to preserving the structural honesty and security of bonded storage tanks. These examinations supply a systematic approach to recognizing prospective issues or weak points in the welds, guaranteeing that any kind of issues are resolved before they rise into significant failings. By conducting routine analyses, organizations can spot rust, exhaustion, and various other types of damage that might jeopardize container performance.In addition, consistent evaluations add to compliance with industry guidelines and standards. Complying with these standards not only minimizes legal visit our website dangers yet additionally enhances the organization's online reputation for security and integrity. Regular assessments cultivate an aggressive safety culture, encouraging employees to recognize and prioritize the relevance of equipment integrity.
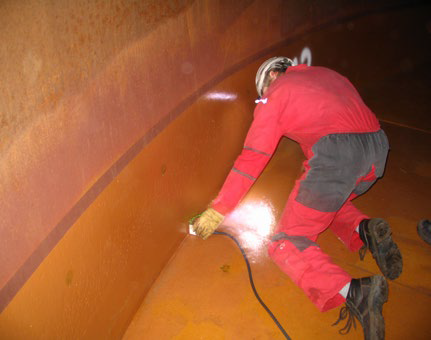
Situation Research Studies and Real-World Applications
Situation researches and real-world applications illustrate the substantial impact of efficient storage tank welding inspection techniques. Adhering to the application of rigorous welding examination procedures, consisting of visual and ultrasonic screening, the facility identified critical imperfections in weld seams that could have led to tragic failings.Similarly, a water therapy plant implemented a detailed inspection program for its container welding operations - anonymous Tank Welding Inspection. By incorporating non-destructive screening methods, the plant had the ability to discover early indicators of corrosion and tiredness in weld joints. This prompt intervention prolonged the life expectancy of the tanks and made sure compliance with safety and security policies, hence securing public health
These situation research studies emphasize the importance of regular and link methodical container welding examinations. By prioritizing these techniques, industries can alleviate threats, boost structural stability, and make certain compliance with safety and security standards, eventually bring about improved operational effectiveness and lowered responsibilities.

Conclusion
In final thought, storage tank welding evaluation is a vital component of keeping architectural honesty and security in industrial applications. Using different inspection strategies guarantees very early detection of possible defects, therefore protecting against disastrous failures.Report this wiki page